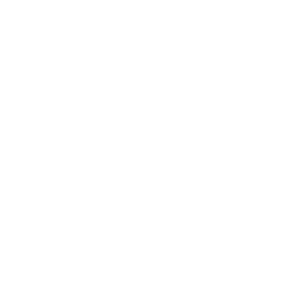
1. Detailed inspection criteria
To promptly identify potential risks and failures and ensure their timely elimination, we have established the following regular inspection system.
During the inspection process, please avoid direct contact with the equipment, especially valves, main circulation pumps, and operating radiator fans, to ensure the safety of personnel and equipment. Inspection personnel must possess relevant professional qualifications and have received professional training on product usage methods and troubleshooting.
We require daily careful observation and recording of the equipment's operating conditions, in-depth analysis and comparison of these data to predict possible operational risks. For any abnormal subtle changes and their development trends, we should quickly identify and take appropriate countermeasures in advance.
2. Key inspection points
2.1 Please carefully observe all operating parameters through the cooling system control panel cabinet to ensure they are within the normal range and there are no abnormal phenomena.
2.2 Check the operating parameters of the main circulation pump, instruments, and equipment one by one to ensure that all parameters are in normal condition and there are no abnormal phenomena.
3. Specific content of routine inspection
3.1 Inspection items
Cooling system: Pipelines, water pumps, water makeup tank level, valve status, pressure gauges, pressure sensors, temperature sensors, flow sensors, power supply and control cabinet, LCD display, container fans.
Cooling tower and external pipelines: Fans, water pumps, water pool level, cooling pipe scaling, pipe connections, valve status, etc.
Refer to attachment 2 "AntSpace cooling system inspection and record form".
4. Important inspection content
Standardized operation card for professional inspection (standby) of water cooling system
No. | Important parts | Quality benchmarks and requirements | Risk detection and prevention measures | Frequency |
1 | Professional inspection of valve internal water cooling system | |||
1.1 | Main circulation pump | 1) There must not be any visible signs of oil or water leakage. 2) There should be no unusual noise or vibration present. 3) The bearing should operate smoothly, free from any abnormal noise or seizing. 4) The inlet and outlet pressure difference should be within the normal range. 5) The area around the main circulation pump should remain dry, and no leakage. 6) When measuring the pump body's temperature using infrared, there should be no abnormal temperature increase. | (1) During the inspection tour, it is crucial to maintain an adequate safety buffer from energized equipment. (2) When conducting inspections, refrain from engaging in any other work, and refrain from moving away from or crossing over the protective fence. (3) Exercise caution when opening and closing equipment doors to prevent excessive vibration. (4) Before entering the equipment area, ensure that you wear a helmet, avoid wearing slippers or high heels, and adhere to the required attire. (5) Strict adherence to the prescribed inspection route is mandatory. The alteration of maintenance site safety measures and the modification of maintenance equipment status during inspections are strictly prohibited. (6) Prior to commencing the inspection, verify that all safety instruments to be used are in working order. | Once every half month |
1.2 | Main Filter | 1) The tank must exhibit excellent sealing capabilities, ensuring no leakage or water overflow occurs. 2) The bolts securing the main filter should be tightly fastened, with no sign of looseness or internal noise. 3) The pressure difference before and rear the main filter should be within the normal range. | Once every half month | |
1.3 | Voltage stabilization system | 1) The pressure in the expansion tank should remain above the standard or normal value. 2) There should be no leakage from pipeline joints or exhaust valves. | Once every half month | |
1.4 | Hydration device | 1) The water level in the makeup water tank should remain within the acceptable or standard range. 2) The PSU of the makeup water pump should function without any irregularities. 3) The valve positions in the makeup water circuit should be in their normal or intended state. 4) The mechanical seal of the makeup water pump should be free from any signs of water leakage. | Once every month | |
1.5 | Sensors | 1) The sensor connector must be securely tightened and devoid of any water leakage. 2) The display value on the sensor panel should be regular and free from any black screen issues. 3) The local display's readings should align with the remote transmission data. | Once every month | |
1.6 | Piping, flanges and valves | 1) The pipeline should exhibit no unusual vibrations. 2) Pipeline and flange joints, as well as drainage valves, should be intact, without any signs of breakage or water leakage. 3) The pipeline and flange should remain unblemished, free from any deformations or distortions. 4) The connection bolts must be securely tightened, gaskets should be undistorted, and the torque line should not have shifted. 5) The valve position should accurately reflect the mode of operation, and the opening degree should not have deviated. 6) The valve position indicator should display normal readings. | Once every half month | |
1.7 | PSU cabinet | 1) Absence of alarm signals and abnormal sounds. 2) The power switch should be in its normal position, with all control handles and knobs correctly aligned. 3) The cabinet status indications must be accurate, reflecting the actual state of the equipment. 4) Components and cables should show no signs of aging or burn paste traces. 5) Infrared temperature measurements of power cables and switchgear components should reveal no local overheating. 6) Terminal wiring should remain intact, with no fallen-off connections or abnormal terminal openings. 7) The inverter panel display should be clear and free from black screen or bad screen phenomena. The signal indicator should be normal, and the control mode should be in its standard position. 8) The radiator fan should operate smoothly, without abnormal sounds or stopping. The filter should remain unblocked. 9) Ventilation style windows should be free of foreign object coverage, ensuring good airflow. 10) The cabinet interior should be free from water and condensation. 11) The lighting function should function normally. 12) The cabinet door should seal tightly, closing properly, and cable holes should be securely sealed. | Once a month | |
1.8 | Control and protection cabinet | 1) Alarm signal absent, devoid of abnormal noises. 2) The power switch is in its regular position, with all control handles and knobs accurately set. 3) The host is securely fastened, fasteners are present and intact, and the exterior is unharmed. 4) The host fan operates smoothly, without abnormal noises. 5) The status indicators on the host indicate normal conditions. 6) All input and output modules and slot connections must be sturdy and dependable, free from bending, deformation, extrusion, and dust accumulation. 7) The cabinet status indication accurately reflects the actual state of the equipment. 8) Components and cables show no signs of aging or burn paste traces. 9) Infrared temperature measurements reveal no localized overheating. 10) Terminal wiring is secure, with no loose connections or abnormal terminal openings. 11) The radiator fan operates smoothly, devoid of abnormal sounds, stalls, or filter blockages. 12) The cabinet is free from water and condensation. 13) The cabinet lighting function should operate normally. 14) The cabinet door seals well, closes properly, and cable holes are tightly sealed. | Once a month | |
2 | Specialized examination of the water cooling system components excluding the valve | |||
2.1 | Piping, valves | 1) The exterior should be devoid of rust, corrosion, and scaling. 2) The pipeline should be free from sand holes and exhibit no water leakage. 3) The indications for pipeline water flow direction, as well as valve opening and closing, should be clear and unambiguous. 4) The valve position should align with the operational mode, and its opening degree should not have shifted. 5) The valve locking device should be intact, with no damage, rust, or corrosion to the lock. | Once a month | |
2.2 | Meters | 1) The meter's appearance should be damage-free, and all joints should be tightly secured with no looseness. | Once a month | |
2.3 | Control cabinet | 1) The display is devoid of alarm signals, and there are no abnormal sounds emanating from the cabinet. 2) The power switch is in its normal position. 3) The indicators on the host, input and output modules, and power modules are all functioning normally. 4) The cabinet status indication accurately reflects the actual state of the equipment. 5) Components and cables exhibit no signs of aging or burn traces. 6) Infrared temperature measurements indicate no localized overheating. 7) Terminal wiring is secure, with no falling off or abnormal opening of the terminals. | Once a month | |
2.4 | Cooling Towers | 1) The cooling tower body is free from leakage, deformation, damage, and rust, among other possible phenomena. 2) The fan motor speed of the cooling tower is normal, with even bearing rotation and no abnormal sounds. 3) The fan blades of the cooling tower are devoid of deformation, cracks, or breakage, and operate with normal running noise. 4) The spray pipe is unblocked, with no breakage, and ensures uniform water flow. There is no overflow in the incoming or returning water, and no suction empty phenomenon. 5) The valve position indications for the import and export of cooling water, water replenishment, sewage, and others are accurate, and the valve locking devices are functioning normally. 6) The fan junction box, safety switch sealing, and rainproof measures are in good condition. The internal wiring is free from overheating, aging, or loose connections. 7) The cooling tower grille is devoid of deformation or water overflow. | Once a month |
5. Cooling tower
The cooling tower requires regular inspections during operation. If any malfunction is found, please replace the parts accordingly.
5.1 Spray Pump
5.1.1 Dimension diagram of spray pump
Outline | Detailed installation dimensions | Liquid inlet and outlet flange size | ||||||||||||||
L1 | H | H1 | L2 | L3 | L7 | L9 | L5 | L4 | L8 | L6 | R | D1 | D2 | D3 | n | dl |
700 | 462 | 232 | 510 | 195 | 402 | 350 | 150 | 170 | 310 | 135 | 6 | 150 | 240 | 285 | 8 | 22 |
5.1.2 Spray pump parts diagram
1. Pump body | 11.Moto | 25.Nut | 34. Impeller spacer | 7 Protection plate | 13. Key (motor) |
3. Impeller | 12. Bolts, washers, nuts | 26. Pipe Plugging | 38. Pump head | 4. Pump shaft | |
5. Mechanical Seals | 15.Base | 30. Bolts, washers | 39. Bolts, washers | 22. Set screws | |
6. Post Circle | 23.Key | 33.Spring washers | 16. Crossed pan head screws | 18.Nut, washers |
5.1.3. Troubleshooting and solutions for water pump failures
Consequences of failure | Reason | Troubleshooting |
Motor doesn't work | 1. The power supply has malfunctioned. 2. The control circuit is defective. | 1. Verify the power supply status - ensure the container's control cabinet is properly powered on or off. 2. Inspect the incoming and outgoing lines - confirm that the three-phase circuit connection sequence is correct, and address any abnormal indications from the container. |
Pump flow is inadequate | 1. The pipeline is obstructed. 2. Air inlet pipe. 3. The motor impeller connection is experiencing water leakage. | 1. Inspect the pump - verify that the impeller disk of the pump is rotating in a regular and smooth manner. 2. Check the pipeline - after removing the water tank strainer, visually inspect the pipeline to see if there are any foreign objects in the pump head, the water tank level is detected by the level meter without replenishment, and there is no vortex in the water tank to absorb the empty situation. 3. Replace the worn wear ring as needed, refer to the instructional video for detailed steps. |
Excessive pump power consumption | 1. Flow rate is too large. 2. The motor bearings have significant wear and tear. | 1. Verify the presence of any overload conditions and take appropriate measures to address the specific overload item. 2. Once the manufacturer has confirmed the extent of wear and tear, proceed with replacing the entire pump. |
Excessive noise | 1. Pump components are damaged. 2. Wear and tear on motor bearings. 3. Air in the pump. | 1. Replace the impeller, which is a component located inside the pump. 2. Once the manufacturer has verified the wear and tear, proceed with replacing the entire pump. 3. To drain the water, use the exhaust bolt located on the flange side of the pump to direct the water out through the bolt hole. Refer to the exploded diagram for detailed instructions. |
Motor is hot | 1. Overloaded current exceeding limits 2. Water inlet flow is inadequate | 1. Verify the system alarm message and ensure that the operating current does not exceed 5% of the rated current value. 2. Inspect the water level in the sink using the supplemental sink water level meter. Ensure that the system indicates a normal water level and that there are no vortexes in the sink, which could indicate an air suction or empty condition. |
5.1.4 Regular inspection and maintenance of the water pump.
Inspection and replacement of the sealing documents - It is recommended to conduct this operation every six months, but if there is shutdown maintenance, winter operation, or operating conditions exceeding technical standards, the inspection and replacement cycle should be appropriately shortened. The sealing part of the fifth component of the mechanical seal is TG brand with a specification of 108-28.
Inspection of bearing rotation normality - It is also recommended to inspect the rotation state of the bearing every six months. However, if there is shutdown maintenance, winter use, or the operating environment is more stringent than the professional technical standards, the inspection cycle should be adjusted flexibly. The bearings are located at the output shaft end and inside the motor, and the selected bearing brand is NSK, with specifications including 6308ZZ C3/5C and 6309ZZ C3/5C.
5.2 Cooling tower fans
5.2.1 Composition of the fan:
The components of a wind machine are:
④ Impeller, which includes blade and hub
Transmission system: includes bearing seat, belt and pulley
⑧ Fan guide barrel
⑩ Protective net
⑫ Motor
Each blade is torque balanced before leaving the factory, and the entire set of wind blades is subjected to dynamic balancing test after assembly. Therefore, the blades cannot be disassembled, disassembled or repaired by yourself during use and maintenance, so as not to affect the balance accuracy of the blades.
Whether the wind turbine is installed on a frame or a foundation, these supporting structures must have sufficient strength, rigidity, and stability. This design aims to effectively absorb and isolate the vibrations generated during the operation of the fan, thus preventing resonance phenomena. At the same time, the foundation structure must not only bear the static load of the fan itself, but also bear the dynamic load and unbalanced inertial force caused by the rotation of the fan and aerodynamic effects.
1. Bolt locking washers | 4. Impeller | 7. Motor fixing nut | 10.Protection grid | 13. Motor fixing bolts |
2. Impeller shaft head bolts | 5. Bushing | 8. Dampers | 11. Protective net fixing bolts | |
3. Impeller fixing nut | 6. Impeller fixing bolt | 9. Protective net fixing nuts | 12 Motor |
5.2.2 Fan operating instructions
5.2.2.1 Operation after running
1) To ensure the stable operation of the fan, we need to closely monitor the vibration level of the fan shaft in all directions, including left-right, front-back, and up-down. The vibration speed must be strictly controlled within the limit value specified by the equipment on which the fan is installed, which is not to exceed 7 mm/s RMS (overall). Once the vibration speed exceeds this standard, the fan must be stopped immediately, and an in-depth investigation must be conducted to determine the cause of the abnormal vibration.
During the initial judgment of whether the fan has any abnormal phenomena, we can listen to the noise and observe the heat dissipation of the entire unit. Only when these initial checks do not reveal any obvious abnormalities can we further measure the vibration level of the fan.
It is worth noting that if the vibration measured by a vibration tester falls within the range of 7-12 mm/s RMS (overall), the fan can be operated for a period of time to resolve the vibration issue.
2) After the fan has been in operation for 50-75 hours, check if the fan blade U-bolt ② is loose.
3) Preventive maintenance plan
(1) Regularly inspect the hardware status inside the fan
The inspection interval depends on the operating conditions of the turbine, ranging from two weeks to six months.
Inspections include:
* Bolt torque
* Corrosion of fasteners
* General condition of blades and blade shaft
To maintain smooth operation and proper balancing of the fan, please regularly clean the dust and dirt on the surface of the fan blades. Once the dirt accumulation thickness exceeds 1 mm, please use a scraper to remove it to avoid affecting the normal operation of the fan due to dirt accumulation.
(2) During the operation of the fan, icing on the blade surface is strictly prohibited. If the fan blades are iced in a stationary state, they must be de-iced before startup. Additionally, it is recommended to regularly remove snow from the blades to ensure the normal operation of the fan.
(3) If the fan is stopped for a long time, it is recommended to start and operate it for 10 to 15 minutes every month to allow the bearing grease to distribute evenly on the steel balls, protecting the bearings. Before restarting, make sure to check the operation of all bearings, and if any are found to be inflexible or jammed, replace them immediately. Furthermore, it is recommended to conduct a routine inspection of the motor every three months.
(4) Important note: During extreme weather conditions such as typhoons, sandstorms, severe convective weather, heavy rain, hail, etc., please ensure to turn off the operating fan to reduce potential damage caused by external environmental factors, thus ensuring the normal service life of the fan.
4) Common causes of fan failures and troubleshooting solutions
Malfunction | Reason | Troubleshooting |
Fan exhibiting vibration and unusual noise | 1. The balance block on the wheel hub is dislodged or the balance is not calibrated after overhaul. (See the exploded view for the location of the wheel balancing block) | Perform wheel rebalancing or conduct an on-site balancing test to ensure proper rotation. |
2. The installation angles of the blades are not uniform, resulting in a blade height difference that exceeds the specified requirements. | Visually inspect the blades to detect any deformations. | |
3.The surface of the blade exhibits uneven adhesion. | Thoroughly clean the blade surfaces to remove any dirt or debris. | |
4.The clearance between the impeller and the wind cylinder is uneven. | Initially check for any friction between the impeller and the wind cylinder, ensuring a uniform spacing (with an error not exceeding 5MM). | |
5.Damage to the spindle bearing. | Upon confirmation by the manufacturer, replace the bearings or the entire machine, if necessary. | |
Unbalanced three-phase current | 1.Imbalance in the power supply voltage. | Measure the power supply voltage and identify the cause of any irregularities. |
2.Failure of the windings. | Determine the cause of any resistance issues and make repairs accordingly (ensuring that the three resistance values are consistent). | |
Motor's rated current exceeds the limit | 1.Intrinsic failure of the motor. | 1. Identify and address the root cause of any issues promptly. |
2.The power supply voltage exceeds the standard voltage. | Measure the power supply voltage to determine the cause and opt for a higher-quality power grid, if possible. | |
Airflow below the required level | 1.The impeller is rotating in the opposite direction. | 1. Adjust the wiring phase sequence to ensure that the fan blades rotate in the direction indicated by the arrow. |
Attachment 1. Reference torque reference table
Torque reference table for carbon steel bolts | ||
External Hexagon Bolts S(mm) | Bolt Diameter M(mm) | Bolt Strength Grade 4.8 Ma (Nm) |
10 | M6 | 3.92 |
13 | M8 | 9.48 |
17 | M10 | 19.1 |
19 | M12 | 32.6 |
22 | M14 | 52 |
24 | M16 | 79.9 |
Stainless steel bolt torque meter | ||
External Hexagon Bolts S(mm) | Bolt Diameter M(mm) | Bolt Strength Grade A2-70 Ma(Nm) |
10 | M6 | 5.6 |
13 | M8 | 13.6 |
17 | M10 | 26.9 |
19 | M12 | 46.9 |
24 | M16 | 117 |
Note: 1. S represents the distance between the two parallel sides of the external hexagon. 2. Ma denotes the torque value required for the bolt, measured in Newton-meters (N-m). |
Attachment 2.
ANTSPACE Cooling System Inspection Log Sheet | |||
Time: | Surrounding Temp: | Surrounding Humidity: | |
Project | Inspection Items | Conclusion | Evaluate |
Cooling system | Main Pump | ||
Water refill tank | |||
Piping, valves and limit markings | |||
Pressure gauges | |||
Pressure sensors | |||
Temp sensors | |||
Flow sensors | |||
Power and control cabinets | |||
LCD display | |||
Container fans | |||
Cooling tower with associated external piping | Fans | ||
Spray water pump | |||
Pool level | |||
Pipe connection port | |||
Valve status | |||
Check conclusion: | |||
Inspector: Verifier: |
Dear Customers,
Hello, May 1-5, 2025 (GMT+8) is China's May Day, and international logistics will be suspended. Our company will suspend shipments on the afternoon of April 30, 2025, and resume warehouse shipments on May 5 (GMT+8). We are deeply sorry for the inconvenience caused to you. Thank you for your trust and support.
Best wishes,
ZEUS MINING CO., LTD
We use cookles to Improve your online experience. By continuing browsing this website, we assume you agree our use of cookies.