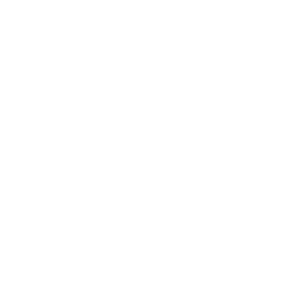
During the soldering process of electronic components on the circuit board of miner, the selection of solder should be strictly controlled. This not only affects the soldering quality of the product but also directly relates to the reliability and service life of the equipment. This article discusses in detail the differences among high-temp solder, medium-temp solder and low-temperature solder from four aspects: melting point, application range, solder composition and soldering effect.
I. Melting Point
1. The melting point of high-temp solder paste is usually above 240°C, and the peak reflux temperature is between 270°C and 360°C. High-temp solder paste is suitable for high-temp reflow soldering processes, ensuring that solder joints can still maintain good electrical and mechanical properties in a high-temperature environment.
2. The melting point of medium-temp solder is between that of low-temperature solder and high-temp solder, and its operating temperature is usually above 220 degrees. Medium-temp solder is more suitable for soldering delicate components such as ASIC chips, because it can provide enough heat for soldering without damaging the chips. Medium-temperature solder can ensure the firmness and reliability of solder joints and reduce the risk of poor soldering.
3. The melting point of low-temperature solder is relatively low, usually below 200 degrees. It is suitable for soldering parts such as microelectronic sensors with low heat resistance. However, low-temp solder may not perform as well as medium-temperature solder or high-temperature solder in terms of soldering strength and durability, especially when soldering larger or more complex components. The solder joints of low-temp solder may fall off when subjected to vibration due to insufficient firmness, which is one of the reasons why some people think that low-temperature solder may lead to repeated repairs after maintenance.
Therefore, if we are soldering some small electronic components with low heat resistance, low-temp solder may be a suitable choice. However, for most hash board repair work, especially when soldering larger or critical components, medium-temp soldering is usually a better choice because it provides better soldering quality and stability.
II. Application Range
High-temp solder: It is mainly used for the circuit boards of miner that require high-temperature soldering.
Medium-temp solder: Due to its excellent properties such as high temperature resistance and oxidation resistance, it is mainly used for soldering components that do not change during the assembly of minier circuit boards and can withstand relatively high temp and pressures.
Low-temperature solder: Due to its characteristics of low melting point and little damage to welded components, it is widely used for soldering parts with low heat resistance on the circuit boards of miner. It is suitable for components that cannot withstand high-temp soldering.
If you need to use solder, you can click here to select it.
III. Solder Composition
High-temperature solder: It is generally composed of metal elements such as tin, silver, and copper.
Medium-temp solder: The alloy composition is generally tin, silver, and copper (abbreviated as SAC). The proportions of these components in the solder alloy are carefully adjusted to achieve the best soldering effect. Solder bars are formed when the proportions of silver, antimony or lead are relatively high. Among them, the addition of silver can significantly improve the electrical conductivity and oxidation resistance of the solder, and the addition of copper can improve the hardness and strength of the solder.
Low-temperature solder: The alloy composition is mainly the Sn-Bi series, among which Sn42Bi58 is a eutectic alloy. Solder bars are formed by adding elements such as bismuth, indium, and cadmium to the solder alloy.
IV. Soldering Effects
High-temperature solder: It is applicable to the high-temperature reflow soldering process, ensuring that the solder joints can still maintain good electrical and mechanical properties in a high-temp environment. It is mainly used in situations requiring high-temperature soldering and for equipment and components that need to work in high-temp environments.
Medium-temperature solder: It has a relatively high melting point and excellent physical properties. It has good solderability, and the solder joints are hard and firm, with few solder joints that are shiny. This enables the medium-temp solder to form stable and reliable solder joints during the soldering process, improving the reliability and service life of the product.
Low-temperature solder: Its solderability is relatively poor, the solder joints are rather brittle and prone to detachment, and the luster of the solder joints is dull. However, due to its low melting point characteristic, the low-temp solder still has wide application value in situations where it is necessary to protect the welded components from high-temperature damage.
There are significant differences among high-temp, medium-temp and low-temp solders. In practical applications, factors such as the soldering temperature, application scenarios, the materials of components and PCBs, as well as costs need to be considered.