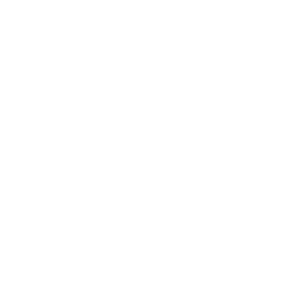
Antminer APW11 Hydro Power Supply Repair Guide
Ⅰ. Maintenance platform requirements
1. Constant temperature soldering iron 120W or above (soldering temperature is 300-350℃). The pointed soldering iron tip is used for soldering SMD components such as chip resistors and capacitors, and the knife-shaped soldering iron tip is used for soldering and replacement of plug-in components (soldering temperature is 380-420℃).
2. The hot air gun is used for chip disassembly and soldering. Be careful not to heat for a long time to avoid PCB blistering (welding temperature is 360-420℃±10℃).
3. Three-phase AC controllable power supply equipment voltage regulator (output 350-420V, current can be limited to 0-20A) for APW11 power-on inspection. If there is no condition, we can also use three-phase mains electricity to string a 100W ordinary bulb in each ABC live wire, and pay attention to safety when controlling the circuit breaker.
4. Electronic load whole machine test (power 7KW, voltage 0-50V, current 350A). If there is no condition, a power resistance load matching the APW11 output DC21.6V can also be made.
5. Multimeter, suction gun, tweezers, ZJ0001000001 or V9 1.2 test fixture plus special PSU test card firmware (if conditions permit, an oscilloscope can be configured).
6. Flux, lead-free tin wire, board washing water plus anhydrous alcohol; board washing water is used to clean the flux residue and appearance after maintenance.
7. Thermal conductive silicone grease (2500) is used for coating the surface and heat dissipation of the ceramic sheet at the bottom of the upper board; AB thermal conductive potting silicone is used for potting and heat conduction between the PCBA MOS and the water cooling plate after maintenance; and thermal conductive silicone (704 silicone) is used for fixing and covering the damaged original glue point of the PCBA component after maintenance.
Ⅱ. Maintenance work requirements
1. Maintenance personnel must have certain electronic knowledge, more than one year of maintenance experience, a certain understanding of the working principle of switching power supplies, and proficient installation and welding technology.
2. Before the product shell is opened to repair the PCBA board, the large capacitor must be discharged. After measuring with a multimeter that there is no voltage (discharge is completed below 5V), welding work can be carried out! Pay attention to confirmation to avoid electric shock.
3. Pay attention to the operation method when judging the circuit components. After replacing any device, the PCB board has no obvious deformation, the pad welding is reliable, and check whether there are open circuits and short circuits in the replaced parts and the surrounding parts.
4. After replacing the key components, the main circuit is checked and measured to have no short circuits and other obvious abnormalities before the AC voltage test can be performed, otherwise there is a risk of explosion.
5. When it is necessary to apply three-phase AC380V voltage to judge the circuit signal, pay attention to the operation protection. When a single PCBA is powered on and outputs no load (no loading), it is necessary to install high-speed fans on the upper and lower jigs to blow air on the power board to dissipate heat on both sides, otherwise the power device will be damaged.
Notes on power supply maintenance:
1. The qualifications of maintenance personnel must meet the specified requirements;
2. The instruments and equipment used for maintenance must meet the specified requirements;
3. The instruments and equipment to be maintained must be effectively grounded, and the maintenance environment requirements must comply with the anti-static requirements;
4. The materials used for maintenance must meet the specified requirements. In order to ensure the accuracy and traceability of the materials used for maintenance, the materials used for maintenance must be the production materials of the corresponding model, and the material replacement requirements must be confirmed;
5. To prevent the possible risk of electric shock, non-professionals should not disassemble the casing;
6. When maintenance personnel open the casing of the power adapter for maintenance, they are required to use a special casing opening machine to avoid damaging the internal components of the product;
7. After the product is opened, the high-voltage capacitor is required to be discharged;
8. The electronic waste fertilizer generated during product maintenance cannot be discarded at will;
9. Defective products must have a maintenance process card to identify the cause of the defect and be placed in different areas;
10. Repaired products must be marked to distinguish them;
11. Repaired products must be placed in the repaired area and require systematic testing before they can be put into storage.
Ⅲ. Principle and structure of the APW111721a power supply
1. Principle overview
1.1 APW11 consists of 2 large boards, 1 water-cooling board plus side and upper and lower shells. The normal single-channel three-phase power input is connected to AC380V, and there are two DC output voltages, namely (OUT2) auxiliary SB12V, (OUT1) main voltage output 17V-21.6V adjustable and controlled by PIC port and miner communication.
1.2 Performance characteristics and scope of use:
(1) APW111721a PSU is a high-efficiency DC power supply designed and produced by Bitmain, with a single three-phase AC input and 2 DC outputs;
(2) DC output 1 (OUT1): 17V-21.6V adjustable output voltage, the maximum current can reach 300A;
(3) DC output 2 (OUT2): 12V fixed voltage output, the current can reach 1A.
(4) OUT1 can output a maximum of 6500W DC power. Under different voltages, the current and power are different. It is suitable for servers and miners and other occasions with strict power requirements;
(5) OUT2 can power the control board and can also meet the needs of DC loads, circuits or other equipment with a voltage of 12V and a current of less than 0.5A.
1.21 APW111721a has the following features:
1) 380-415V AC wide voltage input, frequency 50-60 Hz;
2) Active power factor correction function, PF>0.99 (full load);
3) Adjustable output voltage, remote control;
4) Remote control of power on and off, support communication with host computer;
5) Output ripple less than 1%;
6) With input undervoltage protection, output short circuit protection, overload protection, overtemperature protection;
7) With input power and input current reporting function;
8) Maximum conversion efficiency up to 96%;
9) Small size and high power density;
10) The selection of high-quality devices ensures the stability and reliability of the product through reasonable design, and it can work at full load for a long time in a high temperature environment of 45℃ water temperature and less than 50℃.
1.3 APW111721a Power Supply Appearance Introduction
Placement method for use:
Overall structural appearance:
Front panel
Rear panel
Note: If you need to test the default main output voltage of 21.6V when starting up, you can use an adapter to short-circuit the voltage regulator port EN and GND Pin .
Note: When the output voltage is shorted to around 21.6V, the hash board cannot be connected, otherwise the chips may burn.
1.31 Distribution on the front panel:
(1) 1 LP20 type 4-core semi-metallic flange male AC input interface
(2) 2 water cooling pipe interfaces
1.32 Distribution on the rear panel:
(1) OUT1 output terminal, which can be fixed with 4 M6 screws
(2) 1 4-pin signal terminal
(3) 1 6-pin PCIE terminal with 12V fixed voltage output
1.33 The 4-pin signal terminal is the interface for the external control board to communicate with the power supply. SDA/SCL is the I2C protocol, and the output voltage of the power supply can be adjusted through I2C. EN is the enable signal of the power supply. The control board can enable the power supply through EN, and the low level is effective.
1.34 The model of the AC input terminal on the front panel of the power supply is C14 pin-shaped AC socket snap-on type, which requires the corresponding interface C13 AC input cable to be used in conjunction with it.
1.35 The OUT1 output uses a copper terminal, and the output cable or output copper bar can be fixed on the terminal with M6 screws, which is convenient and flexible to use.
1.36 OUT2 uses 6-pin PCIE5569 connector, 2*3pin.
The 5569 connector and the corresponding connector diagram are shown below:
The PCIE output cable consists of two color wires, the 12V positive cable is yellow and the negative one is black.
6PIN PCIE terminal positive and negative pole definition:
Positive pole: yellow 1, yellow 2, yellow 3
Negative pole: black 4, black 5, black 6
1.4 APW111721a power supply parameter table:
OUT1 | DC Voltage | 17V - 21.6V |
Rated Current (380V input) | 300A | |
Rated Power (380V input) | 6500W | |
Ripple & Noise | <1% | |
Line Regulation | <1% | |
Load Regulation | <1% | |
Setup Time | <5S | |
Short Circuit Protection | >10mS | |
OUT2 | DC Voltage | 12V |
Rated Current (220V input) | 1A | |
Ripple & Noise | <1% | |
Voltage Accuracy | 12.2V - 12.4V | |
Line Regulation | <1% | |
Load Regulation | <1% | |
Setup Time | <5S | |
Short Circuit Protection | >10mS | |
Input | Voltage Range | 380-415V AC |
Frequency Range | 50~60 Hz | |
Power Factor | >0.99 (full load) | |
Leakage Current | <1.5mA (380V 50Hz) | |
Protection | Low-voltage Input | <304V AC |
Output Short Circuit | Yes | |
Overheat Protection | Yes | |
Over-current Output | 300A - 350A | |
Environment | Operating Temperature | -20 - 45℃ |
Operating Humidity | 20% - 90%RH (non-condensing) | |
Altitude | <2000m | |
Structure | Dimensions | 320mmx179mmx63mm |
Net Weight | 5kg | |
Cooling System | Water cooling | |
Inlet temperature | 20 - 35 ℃ | |
Water flow rate | 8L/min | |
Water pressure | <3 BAR |
2. Basic principles of power supply
2.1 Layout of the large board on the power supply PCBA, actual picture display
Layout marking description: three-phase voltage AC input and EMC circuit------PFC and main parallel LLC MOS circuit, main control DSP, 12VCC/auxiliary output port and PIC communication port.
And the following PCBA output board layout, actual picture display
Layout marking description: three-level LLC capacitor to inductor to three-unit transformer step-down rectifier filter output.
If you need to dismantle the board to repair defective products, first remove the board screws, then remove the shell, dig the glue around the corresponding board edge, wait for the surrounding glue and PCB glue to fall behind, and lift the board with force around the PCB. Be careful not to use too much force, otherwise the PCBA will be damaged.
2.2 Working principle of power supply circuit
Schematic diagram of AC three-phase input EMI to PFC circuit:
If you are repairing a defective product with no output, focus on measuring whether F1, F2, F3 fuses, MOV1, MOV2, MOV3, and NTC1, NTC2 are damaged.
For the PFC to LLC MOS main circuit, if the output is abnormal, focus on checking whether the 12 SMD MOS and 6 diodes of the PFC are damaged, and whether the 6 plug-in MOS of the main conversion circuit LLC are broken down or short-circuited.
PFC and LLC drive circuit:
Main control DSP chip, PFC driver, and LLC driver:
PFC PWM and LLC PWM circuits:
2.21 Auxiliary 12V circuit and VCC powering principle
Judge whether there is short circuit abnormality in MOS and other power devices. After power-on, this circuit must work normally before it can supply power to other IC chips. Measure (measurement point is at the bottom of the upper PCB)
(1) TP1-TP2: 365VDC±4.5V (360-371V)
(2) TP3-TP2: -365VDC±4.5V (360-371V)
(3) TP4-TP7: -13.3VDC±0.35V (-13-14.5V)
(4) TP5-TP7: 5.5VDC±0.3V (5.2-5.8V)
(5) TP6-TP7: 12.25VDC±0.15V (12-12.4V)
(6) TP8-TP12: 13.3VDC±0.3V (12.7-14.8V)
(7) TP9-TP13: 14.2VDC±0.3V (13.5-15.8V)
(8) TP10-TP14: 14.2VDC±0.3V (13.5-15.8V)
(9) TP11-TP15: 14.2VDC±0.3V (13.5-15.8V)
(10) TP17-TP21: 13.3VDC±0.3V (12.3-13.6V)
Check whether the auxiliary circuit output 11-12V and each VCC are normal. If abnormal, measure the corresponding Q44, U27, output rectifier diode D25, D9, etc., and whether U12, U14 are damaged.
Note: Under normal use, the probability of damage to this circuit is small.
2.22 Input three-phase voltage and current detection circuit
Input voltage detection circuit, if there is any abnormality, measure whether the VA, VB, VC, N sampling resistors are damaged or short-circuited by soldering.
Input three-phase current detection circuit:
APW11 input current detection circuit:
2.23 PIC control voltage regulation circuit
J16 voltage regulation communication port, if there is any abnormality, check pins 1 and 2 - GND (3.2-3.3V), PICEN 1V is normal. When pins 3-4 are short-circuited, pin 3 is low level, Q32 is not conducting, Q27 is conducting to U33 optical coupler to work; GP1O23 is low level, the main DSP is turned on, and the main output voltage is about 21.6V.
2.24 Output board circuit principle
If the positive and negative poles of the output end are short-circuited, it is necessary to measure whether the low-voltage MOS has breakdown and whether the soldering is reliable.
Overheat protection circuit, this circuit has fewer abnormalities and is not easy to be damaged.
2.25 PCB board screen printing
Side B of the input end board:
Side T of the input end board:
2.26 Output board screen printing
The following figure is the T side. Note: this board has SMD components on the front, and no SMD components on the bottom.
3. Repair steps
(1) Check the appearance of the power supply for serious damage and deformation, and whether the AC socket is damaged.
(2) Check whether the 12V terminal of the AC380V output auxiliary circuit is normal. Use a multimeter to measure whether the voltage of the output J15 terminal is 12V (11V-12.80) to eliminate false detection.
(3) Open the case to check whether the components and solder surface are ignited or burned. Use a multimeter to check whether the three-phase AC input terminal F1, F2, F3 fuses are open. Measure the LLC circuit main switch MOS Q13, Q20, Q3, Q18, Q1, Q8 and the output copper bar and SMD MOS to see if there is a short circuit. If so, check and replace the component, and pay attention to the circuit resistor around the bad MOS tube; the triode may be damaged and needs to be checked and replaced.
(4) If the board needs to be disassembled for repair, after the defective components are replaced and eliminated, the AB glue between the bottom of the PCBA and the water cooling plate needs to be cleaned, and the AB glue is re-adjusted (1:1 ratio) and the glue is poured. The board is installed to ensure the heat conduction of the power MOS. (The thermal conductive glue at the bottom of the PCBA is very important. If the power device has no AB glue, it is easy to damage the MOS when it is powered on.) Refer to the production process documents and assemble the glue pouring operation. AB glue is used according to the materials in the power MOS.
4. Simple judgment and maintenance for the common faults of miner power supply
(1) The control light is not on, check whether the power supply output auxiliary circuit 11-12V is normal.
(2) The hash board has no hashrate and reports V:1. Remove the power supply, disconnect the output copper bar and the hash board, short-circuit the power signal terminal EN--GND separately, and measure whether the output copper bar has about 21.6V. If the voltage is normal, it is necessary to test the load capacity (use electronic load, output 21.6V can add 300A is normal). Otherwise, the power supply is poorly loaded, and check whether the high-voltage MOS on the upper board is damaged.
(3) The power supply has no main output, check whether the positive and negative poles of the output copper bar are short-circuited; if there is, measure the low MOS. If there is no abnormality, test whether the upper board components are damaged.
5. After the power supply is repaired and tested to be normal, the short-circuit signal output is about 21.6V, the water cooling temperature is between 20-45, and it needs to be aged and run for 2 hours with a rated load of more than 80% (280-300A) before it can be used by the client.
Attention: The APW11 water-cooled power supply can only work when the upper and lower boards are connected together. Therefore, after removing the boards for maintenance, if we need to test, we need to place thermal pads and heat sinks at the bottom of the PFC MOS and LLC MOS boards to allow the power devices to dissipate heat before powering on. If we should test for a long time, we need to connect a water cooling system for heat dissipation.